Time to choose: The importance of feasibility studies in coiled tubing drilling
While on-the-job learning is undoubtably a valuable road to building experience, knowledge and expertise, it is also essential that professional operators in most any field of industry are able to conduct pre-deployment simulations of their intended activity. For example, an airline pilot would have spent many hours in a flight simulator before taking the controls of an actual airplane. Similarly, in oilfield operations involving extremely high pressures, and use of hazardous chemicals and complex systems, the ability to digitally simulate specific operations and undertake feasibility studies is essential for both safety and commercial gains.
Application challenges. A feasibility study can be considered as negative proof. In other words, it is a demonstration that a particular problem cannot be solved, as described in the claim. Therefore, one of the most important factors in these early-stage analyses is to identify when not to use certain technology. This is especially relevant for broad-use technologies, such as coiled tubing drilling (CTD), which can be used for a broad range of applications but, due to its complexity, should certainly not be considered a one-size-fits-all approach to oilfield operations.
The benefits of CTD and, specifically, its cost advantages over conventional drilling in certain applications, are well-documented. In remote operations, for example, the low mobilization costs and smaller crew sizes required by CTD can result in a higher return on investment by delivering the same production rates as conventional drilling—but at an overall lower project cost. In other applications, such as drilling depleted reservoirs underbalanced with a two-phase fluid system of water and nitrogen, a higher investment is required, but the payoff is production levels that could not be achieved if drilling overbalanced with a conventional rig.
The core advantage of coiled tubing when drilling is pressure control. Continuous pipe and equipment rated for 15,000-psi wellhead pressure as standard gives considerably more flexibility in terms of drilling both underbalanced and at balance with formation pressure, and provides scope to adjust the well parameters on the fly, based on live observations while drilling the hole section, Fig. 1. For example, when drilling through a highly productive fracture. When drilling underbalanced or at balance on a conventional rig, the rotating control device (RCD) has a much lower pressure rating than the rest of the pressure control equipment. A standard RCD has a pressure rating of 2,000 psi static, 1,200 psi when stripping, and even less when drilling ahead. However, on a coiled tubing unit, the rotating control device is replaced by a stripper that is capable of operating up to the same pressure as the blowout preventers in most instances, meaning that CTD has the safest possible set-up from a well control standpoint when drilling underbalanced.
Tool benefits. While it is simple to reel off a long list of the potential benefits that CTD technology can provide to users, that is not necessarily helpful from a sales perspective, because while all of these benefits are achievable in the broadest sense, they may not all be achievable in every specific application. In other words, while something may be feasible, it is not always desirable in the specific circumstances, and to ignore that fact would be a disservice to the end-client. Therefore, the challenge for any CTD sales representative is to work with the client to understand and identify the correct technology for the application and, crucially, the right configuration of that technology in order to optimize the outcome. The feasibility study is the first stage in this process and must take into account both the technical and commercial feasibility of the proposed solution.
Let’s assume for the sake of this article that the project scenario on the table is to re-enter and drill gas wells underbalanced, using CTD to maximize productivity while preventing damage to the formation. If we re-visit our earlier analogy of a feasibility study being like a “negative proof,” then, in this case, the claim we are attempting to disprove is that CTD is the technology most likely to achieve success and maximize return on investment for this project.
A fundamental first step is to fully understand the clients’ rationale for wanting to utilize CTD technology for their project, as well as the specific project objectives, challenges and parameters involved in their operation. This will involve consideration of any access restrictions, pad size, and the general drilling background in the target formations. Usually, this initial discussion is enough to determine whether there is a suitable application for CTD and, assuming this is indeed the case, the next step is to identify the level of detail required from the study, which in turn will determine how deep into technical analysis to go.
The main components of the technical analysis for an underbalanced CTD feasibility study are: 1) wellbore hydraulics modelling; 2) coiled tubing modelling; and 3) equipment specification and cost estimation. But before carrying out any hydraulics modelling, a draft trajectory should first be created. This will produce a set of constraints and challenges that will inform the well design. For example, can the well be sidetracked and landed within the target formation, or are there multiple formations to drill through? For each formation required to be drilled through, the wellbore stability and safety implications must be assessed. At this point, it is possible to begin to build a picture of the overall project duration and budget. As the hydraulics modelling is carried out, these figures can be refined further to provide a more accurate assessment for the operator.
Hydraulics models are built inside a steady-state multi-phase flow modelling software, and a critical factor analysis is carried out to provide an idea of the fluid type and weight that will be used. At this stage, it is important to determine if a single-phase fluid, such as water or brine, will be used, or a two-phase fluid such as co-mingled water and nitrogen. As modelling progresses, the operational limits of the fluid type and weight and the well productivity can be understood with greater certainty, which allows a tubing forces analysis to be carried out, to identify the coil size required to achieve the target lateral length. This is crucial, as the design of the coiled tubing affects the hydraulic response of the well and vice versa.
For example, coiled tubing with a larger outer diameter will reduce the annular space and, therefore, increase the bottomhole pressure and annular velocities, both of which are critical factors to consider in the well design. Moreover, the injected fluid and the produced gas volumes will affect buoyancy, annular pressures, and pump pressures, which will, in turn, affect the buckling limits, available weight-on-bit, lateral reach, overpull and coil life.
Now that the optimal coiled tubing size has been identified, the models are run to understand the relationships between injected fluids, reservoir productivity, circulating rate and wellhead pressure (see Figs. 2, 3 and 4). The key objective here is to determine how to maintain safe control of the well throughout the operation. In gas systems, transient effects and varying wellbore pressures can be difficult to control and may trigger inadvertent overbalanced situations and increase the chance of hole collapse.
Coiled tubing has a distinct advantage over conventional rigs here as, once stable circulating parameters are obtained, then they can be maintained for the entire hole section. In underbalanced operations, this is achieved using equipment that controls flow and pressure, with secondary well control provided by the BOPs. Therefore, it is essential to gain a full understanding of the potential gas production, in order to inform the selection of fluids and equipment needed to drill the well safely.
Something to note here is that the wellbore hydraulics, like the coiled tubing string design and trajectory, will limit the overall lateral length that can be achieved. For example, it is possible to be underbalanced at the heel of the well and overbalanced at the toe. This can result in losses or overpulls at the toe, due to poor hole cleaning when the well is producing as expected from the heel. Although it can be controlled to a certain extent through operational procedures (e.g., flowrates and optimized fluid weights) and well design (e.g. hole size and casing size), it is an important factor to take into account during early stage planning.
Now that the hydraulics modelling has enabled the critical factors to be pinpointed, it is possible to revisit and optimize the coiled tubing models. By combining the two sets of modelling data, we can now calculate accurate estimations of the final lateral reach achievable, as well as well productivity and expected coiled tubing grade. This is a significant stage of the feasibility study, from both an engineering and cost/durability perspective, because now a draft design can be specified. This will include details of the equipment requirements and, crucially, will enable an outline project budget to be made.
A significant proportion of the costs will be incurred in advance of the project and are relatively easy to budget for, such as feasibility studies; engineering design and planning work; coiled tubing purchases;, and mobilization costs. However, it is important that the feasibility study also highlights the factors that could cause a variation in that cost, and that it anticipates the potential extent of this variation.
One final element of the feasibility study that warrants a mention is the consideration of real-life events that could affect the outcomes predicted by the modelling. In other words, we need to ensure that the study takes into account the “human” factor. Computer modelling, done right, can provide a solid solution in theory, but whether that solution is achievable will be determined by less predictable factors, such as personnel experience and potential equipment failure. Therefore, the feasibility study should address various “what if” scenarios, in order to prepare for the unexpected and ensure that all and any safety concerns are sufficiently mitigated for.
VALUE DELIVERED
To reiterate the point made earlier in this article, CTD is a complex technology, the benefits and outcomes of which must be assessed on a project-by-project basis, in order to be fully realized. While any drilling project will involve significant unknowns, mitigating or controlling the outcome of those critical factors is most effective when done from the very beginning to ensure that coiled tubing is indeed the right technology for the application. The feasibility study is, therefore, arguably the most important stage in the project planning process. It is by maintaining a heavy focus on engineering design and planning in this early stage of a project that operators and service providers can maximize the chance of success.
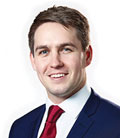
- Bringing geosteering efficiency to coiled tubing drilling operations on the North Slope of Alaska (March 2025)
- Overcoming real-time LWD limitations of longest horizontal drilling: A unique experience from Abu Dhabi (March 2025)
- Drilling advances: Could drilling save the world? (March 2025)
- Integrated managed pressure drilling system improves insights for enhanced performance (January 2025)
- Drilling advances: How to make the pie bigger (January 2025)
- Integrated automation technologies and proactive support network optimize drilling performance (December 2024)