Reducing conservatism and increasing service life of subsea BOPs with novel strain sensor
A significant portion of subsea BOPs in harsh environments boasts equipment to monitor the loads on subsea wells imposed onto the wells through subsea BOP connectors. The main driving force is to manage the loads imposed in subsea structures, due to vessel movement and wave loading on the riser itself. To keep track of these movements, loads, and fatigue accumulation on subsea wellheads, on the Norwegian Continental Shelf (NCS), more than half of semisubmersible drilling rigs in the region boast equipment to measure motion and load on the subsea BOP.
Typically, motion sensors are used to monitor the motions of the lower part of the riser and BOP stack. Then indirect methods, including knowledge of the system parameters, such as tension weight and drag coefficients, are used to establish the overall loads. Alternatively, direct measurement of the load, using strain gauges or linear variable differential transformer technologies (LVDTs), has proven challenging, due to time-consuming installation, fragile measurement equipment, and difficulties finding suitable areas to mount the sensors.
4Subsea, a leading provider of digital technology and services to the energy and maritime sector, has developed a novel sensor technology to overcome these shortcomings. It allows for accurate measurement of strains, in a wide measuring range, as part of its Subsea Wellhead Integrity Monitoring (SWIM) system.
QUALIFICATION
Small enough to be mounted behind the bolts/nuts on an 18¾-in. BOP flange neck, the sensor (using 4Subsea proprietary technology) is a low-power consumption unit, designed to be used for load measurements on subsea structures, Fig. 1. In contrast to existing measuring equipment, the compact device is robust and easy to install. Importantly, it can be used to increase the accuracy, and reduce unnecessary conservatism, in the measured wellhead loads.
Therefore, it may reduce the need for expensive load-reducing measures or disconnects. It consists of a stainless-steel housing with a moving plate connected. The sensor rests at the surface of the component to be measured at three spikes that will follow the surface of the component. The distance between the moving plate and the main housing is measured through a low-power sensor. One typical use of the sensor is to monitor axial and bending load on an 18¾-in. 15K API flange neck on a subsea BOP, Fig. 2.
When used in subsea strain monitoring, a standard sensor kit will be mobilized. A strain measurement kit comprises the following main components (Fig. 3), and its specifications are detailed in Table 1:
- Four retrofittable SMS strain sensors. These devices are designed to be placed around the circumference of a pipe segment. The sensors are fitted with magnets, which are only intended to simplify installation of the sensor. It is fixed to the surface, using a Kevlar strap designed to fit in the groove on top of the sensor.
- Strain module. The battery-powered device is connected to each of the sensors through a cable that also connects the strain busmaster. The purpose of the strain module is to gather data and provide power to the strain sensors.
- Strain busmaster. Again, powered by battery, this device consists of a standard SMS motion sensor that is capable of data storage. Its purpose is to store the strain data and possibly transfer those data to a wireless ROV-carried subsea modem.
As the sensor is designed to be used for the fatigue monitoring of subsea structures, it has been subjected to an extensive test program over three different categories: single-sensor prototype tests; sensor FAT tests; and system tests. The program focused on its performance in measuring peak-to-peak range in a cyclic load. Several different test set-ups were used throughout the qualification testing.
Single-sensor prototype tests. The purpose of the single-sensor prototype test is to verify the concept and prove that the sensor performs, as intended, within the temperature and pressure ranges specified in the sensor specifications. The following tests have been performed with acceptable results:
- Sensor accuracy/linearity–verify performance within the sensor range of ±2700 µ strain.
- Sensor environment–performance in air, seawater and fresh water.
- Pressure–performance when pressurized up to the sensor pressure rating.
- Long-term testing–stability of the sensor.
- Functional tests–the effect of functional loads. For example, the effect of a normal load from the fixation strap, as well as the effect of loads on the cable.
Sensor FAT tests. The purpose of the FAT test is to ensure that the sensors are working properly before shipment. Acceptable results from the following tests are required before the sensor is transported. Each sensor is calibrated, using the single-sensor static rig. This consists of a plastic material, polyoxymethylene (POM) table with a sensor fixation bracket, a center bolt with a micrometer screw in one end and a dial gauge in the other. The sensor housing is fixed to the table, and the spike in the moving plate is fitted in a hole in the center bolt. This way, the moving plate can be moved in precise steps while data are logged.
All four sensors in a kit are then mounted on a steel plate test rig, in which a steel plate is terminated at one end, with a weight or a stepper motor providing load at the other end. Up to four sensors can be mounted at the same axial position. The test rig also can be placed in a pressure chamber or in a water tank. It is then checked, so that the sensor measurement of all four sensors is linear and provides correct sensitivity. To test pressure, the kit is subjected to pressure tests up to the rated pressure. It also undergoes a helium leak test, in which a helium sniffer is connected to the sensor compartment that is placed in a helium-filled plastic bag. A vacuum is applied, and the sniffer will detect possible leaks, if helium molecules enter the compartment.
Sensor system tests. The purpose of the sensor system tests is to gain experience on the measurement of dynamic bending moment variations. The following tests were performed:
- Pipe bending. Two strain sensors were fixed on the tensile and compressive side of a 14-in. steel pipe. This pipe was subjected to a bending load through a three-point bending test set-up. The measured strain was then compared to the applied load.
- Subsea prototype test. An early prototype of the sensor kit with four sensors was mounted over the gap of an 18¾-in. A 15K API flange on a subsea BOP at an approximately 300-m water depth. The main purpose was to gain experience with the sensor technology during subsea operations. The prototype sensors logged data for a total period of eight months.
- BOP tension test. During one of the first campaigns with the strain sensors on a subsea BOP, the riser top tension was changed stepwise between given tension levels.
The measured tension from the strain sensors is shown in Fig. 4.
Calculation of bending moment and tension. Theoretical strain to tension and moment for a straight pipe. The purpose of the strain sensor is to measure the dynamic variation of the axial tension and the bending moment of a subsea steel structure. The measured strain must, thus, be translated into system loads. Axial strain in a straight pipe, when subjected to tension and bending, is illustrated in Fig. 5. Standard regression algorithms can be used to estimate the bending moment and tension time series.
Theoretically, three sensors are enough to extract the bending moment and tension for a pipe cross-section. As the strain kit consists of four sensors, the quality of the signal for the different sensors can be checked by comparing the bending moment for all combinations of three sensors, with the bending moment using all four sensors. An example of such a check is shown in Fig. 6.
Use on an API 18¾-in. 15K API flange neck. The strain sensors were mounted on an API 18¾-in. 15K flange neck with a short straight section, Fig. 7. The axial strain along the surface was affected by local warping of the flange. This effect must be accounted for, if strain measurements on the API flange neck are to be used to measure the loads through the flange. An FEA model is, hence, established of the given flange hub and adjacent structures.
The model is then loaded with different combinations of tension, pressure and bending moment. The relative displacement of a two-node pair, with distance equal to the axial distance between the sensor spikes, is then used to calculate the average strain over the sensor length, Fig. 8. The strain along the surface of the hub area, where the strain sensors are located, is presented in Fig. 9.
The black error bars on the average strain indicate the position of the sensor spikes. This strain varies significantly along the surface, with the maximum strain near the flange side of the hub. The average strain over the sensor length is also shown. The absolute value of this shows a clear dependence on where the sensor is placed along the hub. This is due to the warping of the flange, resulting from pre-loading of the bolts. If the strain due to preload is removed, the measured strain becomes independent of the location of the sensor along the flat part of the flange hub. The variation in measured strain for different sensor locations is less than 2.5% for all possible locations along the flat part of the flange hub. The same picture is also seen for bending load. The sensor strain at eight different locations for the flange loaded with pure bending moment is shown in Fig. 10.
P1 to P4 are sensor locations on the compressive side, while P5 to P8 are sensor locations on the tensile side (see sensor locations in Fig. 9). The average strain from the four locations on the tensile and compressive side, respectively, is then scaled with the scale factor and compared with the theoretical strain for a straight pipe.
The nominal strain, defined as the strain without warping effects, can be calculated by the introduction of a geometric scaling factor. The nominal strain, calculated as the average of the strain at the four locations multiplied with the gain factor, is also shown in Fig. 10, together with the theoretical strain for a straight pipe. The typical interface for integrity monitoring of subsea wells is the wellhead datum. The fatigue capacity of the well is given in terms of bending load versus number of cycles to failure curves (MN-curves). It is, hence, needed to transform the measured load down to the wellhead datum. This is done under the assumption of a constant ratio between the shear force and the bending moment through the BOP. The wellhead bending moment can then be calculated.
Results and experience from operation. The first sensor kit was installed on a BOP, on the NCS, in June 2019 as a part of 4Subsea’s Subsea Well Integrity Monitoring system (SWIM). This employs retrofittable subsea sensors to monitor and measure stability, load, fatigue and structural integrity of the wellhead system during drilling operations. Advanced algorithms and machine learning, combined with deep domain expertise, are used to analyze fatigue damage accumulation, well support and structural integrity. These critical data can be used to assess performance, provide prediction analysis and, importantly, rapidly inform decision-making to reduce risk and cost.
It also can be extended to provide live monitoring of drilling risers and conductors with attachment to the rig pod umbilical. The smart system can detect and manage shallow gas/shallow water, structural failures in the wellhead, and conductor instability issues. With SWIM, operators can re-use critical wells and maximize the lifetime of wellheads by scheduling drilling operations, based on well criticality, historically accumulated load on wellhead, and predictive models. This can assess the expected load on the wellhead from the next drilling operation, based on weather forecast.
The new sensor extended the capabilities of the SWIM system, enabling a more direct extraction of the loads on the subsea wellhead. An example signal from this first system is presented in Fig. 11.
The plot shows the LRMP angle in the roll direction from the motion sensor, compared with the measured bending moment around the local y-axis from the strain sensor kit. The two signals coming from two independent sensors correspond well. This fact supports that the two sensors are capturing the actual system behavior. Over the last seven years, the SWIM system has developed and improved the algorithms for wellhead load monitoring. Until this point, it has relied on an indirect measurement method, where a combination of system knowledge and motion sensors are used to establish the well stiffness and the wellhead bending moment.
The current SWIM indirect method relies on system parameters, such as weights, dimensions, and hydrodynamic properties of the subsea stack. A comparison of the wellhead bending moment one-hour standard deviation is presented for three different drilling campaigns on the NCS, using two different semi-submersible drilling rigs depicted in Fig. 12. Each point in the plot represents one hour of operation, calculated using the indirect method and the strain sensor kit.
In general, the results from the two methods correspond well. The indirect method tends to be on the conservative side. This is as expected, as the input parameters used in the indirect method are similar to the input to a design analysis. These parameters will typically be selected on the conservative side. The introduction of direct load measurement will reduce this conservatism
However, the resolution in the strain measurements seems to be higher than what the indirect method provides. This is indicated, as the indirect strain measurements seem to reach a “floor” value at a higher bending moment than the strain sensor. The rotation of the BOP stack is getting close to the sensor noise level, and the resulting bending moment will be dominated by sensor noise. For stiff wells on deeper water depths, the introduction of a direct load measurement system will be a significant improvement.
CONCLUSIONS
The new strain sensor is proven to work as intended. This has been verified through qualification testing and comparison with the indirect method through the first couple of campaigns. Direct measurement of the bending load also enables new possibilities. For instance, using the comparison between the indirect and the direct method to further improve the input parameters to predictive riser analyses.
The input parameters in the indirect method are similar to the input data to predictive riser analyses. By comparing the direct measurements and the indirect method over time, more accurate input parameters can improve future predictive models. In addition, the strain sensor kit can be used to measure the dynamic tension variation on the BOP connector. This can be used to document the actual tension variations introduced through the riser tensioning system.
ACKNOWLEDGEMENT
This article is an abridged version of OTC paper 30862, presented at the Offshore Technology Conference, Houston, Texas, May 4-7, 2020. Due to Covid-19, the physical event was not held. The official proceedings were published online May 4, 2020.
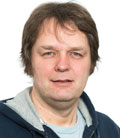
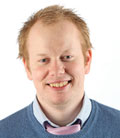
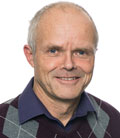
- Executive viewpoint: Advancing offshore crane safety through collaboration (March 2025)
- Bringing geosteering efficiency to coiled tubing drilling operations on the North Slope of Alaska (March 2025)
- First Oil: Deepwater Development conference highlights renewed interest in that sector (March 2025)
- Overcoming real-time LWD limitations of longest horizontal drilling: A unique experience from Abu Dhabi (March 2025)
- Drilling advances: Could drilling save the world? (March 2025)
- What's new in exploration: Gulf of what? Mar del Norte ~1519? Gulf of North America? (March 2025)