Digital transformation: Accelerating productivity, sustainability in oil and gas
Oil and gas companies are under enormous pressure to work in more efficient, responsible and sustainable ways. Even with calls to cut emissions, though, the appetite for fossil fuels seems insatiable. During September, Saudi Aramco CEO Amin H. Nasser shared that demand may rise to 110 MMbopd by 2030. A bullish outlook means oil and gas companies must find efficiencies elsewhere, if they are to meet climate targets set out in the Paris agreement. All while keeping quality levels high, employees safe, and global demand met.
OPPORTUNITY FOR OIL AND GAS COMPANIES TO CATCH-UP
Indeed, by upgrading legacy architecture and deploying a mix of hardware, software, and connectivity solutions, the industry can maximize its gains from Industry 4.0. As eager as the industry is for the benefits of digital transformation, results from the Industry 4.0 Maturity Index would show there’s room for improvement. The survey of 500 companies in five key markets reveals that oil and gas companies are lagging behind industries, such as fabricated metals and electronics/appliances, when it comes to their digitalization journey.
The good news is that a robust toolbox of digital technologies already exists. Think artificial intelligence, augmented reality, and deep data insights—available today to help industries develop digital capabilities at scale.
TOOLBOX OF DIGITAL TECHNOLOGIES
Extracting oil and gas and transporting it to refineries over thousands of miles is an immense undertaking. Refineries, themselves, cover a large area with miles of pipes and specialized equipment. The working environments are often hazardous, and fluctuations in the supply chain are a constant concern.
This is where digital transformation can help. Tools, such as IoT devices, automated robotics, and digital twins, enable oil and gas providers to align their IT (Information Technology) and OT (Operational Technology) environments, improving business operations.
IoT devices are being deployed at industrial sites as an extension of the instrumentation that already exists in the oil and gas industry. Consolidation of all industrial protocols into one platform that backhauls the information into the relevant systems is becoming a reliable and secure way of connecting and collecting data towards a fully automated site.
Improved situational analysis is one benefit – and there are dozens of sources for the data. By combining IoT sensors, wearables, and body cam footage with real-time analytics, it is possible to follow the exact location, exposure and movement of employees and assets, as well as monitor vital health statistics—helping to keep staff out of harm’s way. This can lead to better decision-making, laser-sharp preparedness, and faster response times.
Drones are an especially powerful tool to elevate intelligence and safety. Utilizing drones equipped with thermal cameras for inspection and maintenance at oil rigs, pipelines and plants can keep workers out of more hazardous sites. Linking these drones to a flare stack can help to monitor excess hydrocarbon gases—assisting in efforts to meet pollution caps—as well as make it easier to identify a leak in a pipeline.
More tools are available to remove staff from harm’s way while doing their jobs. Robots like the Boston Dynamic Dog can assess the danger level and conditions in hazardous areas. Equipped with sensors that monitor and measure, robots can detect different elements like gas, water, and other threats or access pipes in challenging locations during corrosion inspection.
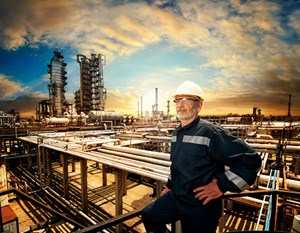
INDUSTRIAL METAVERSE AT WORK
Though augmented reality and what is being called the “industrial metaverse” may seem radical and far from where we are today, applications within the oil and gas industry are unfolding. Within the industrial metaverse, human capabilities can be augmented to naturally interact with the digital world, and real-world things can be dynamically represented in the digital world to also interact with them. This will bring a new level of control and monitoring of physical assets and operations.
One of the earliest applications of the industrial metaverse is digital twins which help oil and gas companies optimize their operational efficiency and spend time on what really matters. By deploying a digital twin—or copy—of a network or industrial asset, companies can monitor performance, gaining real-time end-to-end visibility into the productivity and efficiency of their systems and processes. This can enable them to anticipate and unblock bottlenecks, detect capability gaps, and identify areas that require additional resourcing.
Digital twins also can help companies simulate scenarios and plan accordingly before real-world implementation. For example, digital twins can monitor network performance as well as mobile devices and IoT sensors to identify and narrow down or predict errors at the network or device level. In parallel, crisis planning for cyberattacks, natural disasters or other hazards is now possible—realistically simulating worst-case scenarios, so staff are better prepared.
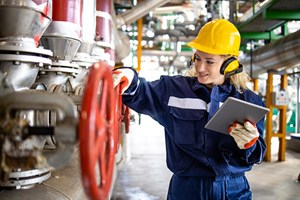
THE JOURNEY TO DIGITAL TRANSFORMATION
Making digitalization and innovative applications happen requires robust private networks. The advanced connectivity provided by 5G private wireless has become a foundational platform for digital transformation. With native reliability, quality of service, and security, private wireless networks can provide the prioritization per application needed, a multi-service approach, and real-time data gathering for powerful automation capabilities and predictive analysis.
The proliferation of IoT sensors and intelligent devices, together with applications for remote operations and automation, is an oil and gas operator’s dream scenario. By generating more operational and environmental data, operators can become data-driven—even in the most remote or hazardous locations.
A modernized communications infrastructure that can sense, think and act, and enable the industry to build the resilience and digital capabilities it needs, is a must. And it is here. Available now to future-proof oil and gas operations, keep workers safe, and ensure the environment is protected.
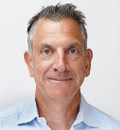
- Monetizing flare gas in North America onshore, in practice (March 2025)
- Permanent P&A performed on coiled tubing, setting rock-to-rock barriers and protecting potable water sources (March 2025)
- The transition to Net Zero emissions: An upstream technology outlook (March 2025)
- Bringing geosteering efficiency to coiled tubing drilling operations on the North Slope of Alaska (March 2025)
- Decarbonizing Scope 3 emissions: The responsible approach to energy travel (February 2025)
- Wood’s Hall sees oil and gas projects progressing while energy transition work gains scale (February 2025)
- Subsea technology- Corrosion monitoring: From failure to success (February 2024)
- Applying ultra-deep LWD resistivity technology successfully in a SAGD operation (May 2019)
- Adoption of wireless intelligent completions advances (May 2019)
- Majors double down as takeaway crunch eases (April 2019)
- What’s new in well logging and formation evaluation (April 2019)
- Qualification of a 20,000-psi subsea BOP: A collaborative approach (February 2019)